A Comprehensive Guide to the Types of Ceramic Layer on the marketplace
Ceramic finishings have arised as a crucial solution across various markets due to their one-of-a-kind properties and applications. As we check out the distinct attributes and applications of these coverings, the effects for performance and longevity come to be significantly evident, raising inquiries about which kind might ideal fit your demands.
Comprehending Ceramic Coatings
Ceramic coatings are advanced safety services that have actually obtained appeal in different industries, particularly in automobile and aerospace applications. These coverings include a liquid polymer that, when healed, forms a resilient, hydrophobic layer on the surface area of the substrate. This layer gives enhanced resistance to ecological impurities, UV radiation, and chemical exposure, thus prolonging the life and aesthetic appeal of the underlying product.
The basic element of ceramic finishes is silica, which adds to their hardness and resilience. The application process commonly involves surface area preparation, application of the finishing, and curing, which can be achieved via warmth or UV light. As soon as treated, ceramic finishes show extraordinary bonding residential or commercial properties, permitting them to adhere highly to a selection of surfaces, consisting of metals, plastics, and glass.
In enhancement to their safety features, ceramic finishings likewise provide ease of upkeep. Their hydrophobic nature reduces the adherence of dust and grime, making cleansing simpler and much less frequent. Overall, the fostering of ceramic finishes stands for a considerable development in surface area security technology, giving both useful and visual benefits throughout several sectors.
Kinds of Ceramic Coatings
Different kinds of ceramic coverings are readily available, each made to satisfy certain efficiency needs and applications - Car Detailing. One of the most common types consist of:
Silica-based Coatings: These layers primarily consist of silicon dioxide and are recognized for their longevity and chemical resistance. They are commonly made use of in automotive and industrial applications.
Titanium Dioxide Coatings: Popular for their photocatalytic properties, titanium dioxide finishings are usually used in environments where self-cleaning and antifungal homes are preferable, such as in structure materials and automotive surfaces.
Zirconia Coatings: Characterized by their high-temperature stability and thermal resistance, zirconia coatings are utilized in applications such as turbine engines and high-performance automotive elements.
Alumina Coatings: Showing superb firmness and thermal stability, alumina finishings are frequently used in wear-resistant applications, consisting of reducing tools and industrial machinery. - Car Detailing
Crossbreed Coatings: Integrating the homes of numerous products, hybrid finishings supply improved performance features, making them appropriate for special and demanding applications.
Each sort of ceramic covering offers distinct objectives, enabling customers to choose the most ideal service based upon particular environmental problems and performance demands.
Advantages of Ceramic Coatings
Coatings play a crucial duty in enhancing the efficiency and durability of surfaces throughout different industries. Ceramic finishings, in specific, deal countless advantages that make them significantly preferred among manufacturers and consumers alike. Among the main advantages is their exceptional click for source sturdiness. These layers are immune to scratches, chemicals, and UV rays, making certain that the underlying surface continues to be safeguarded gradually.
Along with longevity, ceramic coverings supply superb hydrophobic buildings, allowing for simple cleaning and upkeep. This water-repellent nature minimizes the adherence of dust, grime, and other pollutants, which can prolong the visual allure and functionality of the surface area. Ceramic layers can dramatically enhance thermal resistance, making them perfect for applications that endure high temperatures.
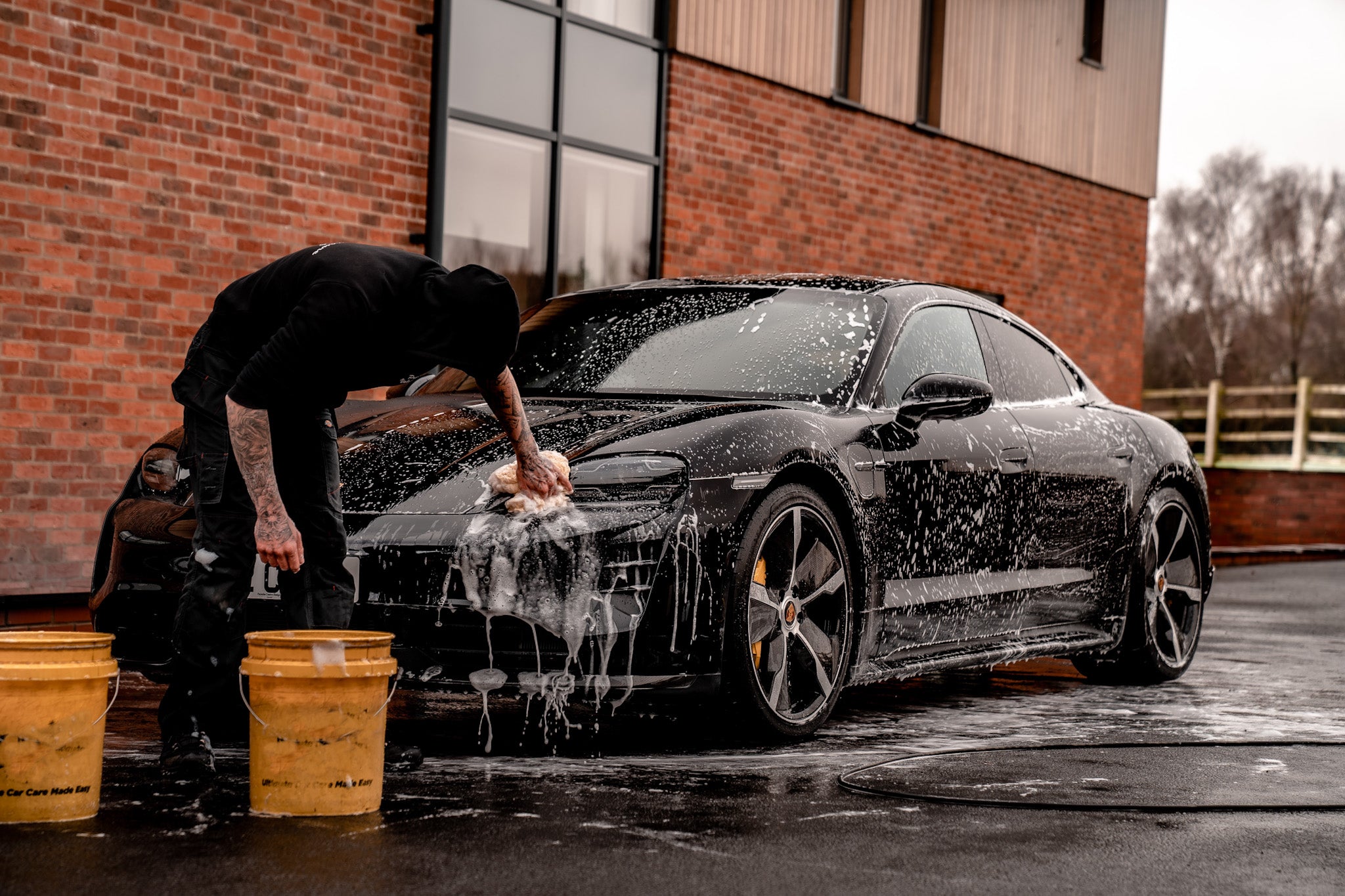
Application Refine
When applying ceramic coverings, a thorough approach is crucial to attain optimal outcomes. A clean surface area makes certain proper adhesion of the finishing.
Once the surface area is prepped, the following step is to use the ceramic finishing. The coating should be used in thin layers, as thicker applications can lead to unequal coatings.
After application, the layer requires a specific curing time, usually varying from a couple of hours to a complete day, relying on the item. Throughout this moment, it is essential to stay clear of direct exposure to moisture or pollutants. A gentle buffing might be necessary after curing to improve the gloss and eliminate any kind of high places. Complying with these steps carefully will make best use of the performance and long life Your Domain Name of the ceramic layer, providing a durable protective layer for the surface.
Maintenance and Long Life
To ensure the durability and performance of a ceramic finishing, normal maintenance is necessary. Ceramic coverings, understood for their resilience and safety qualities, need specific care regimens to maximize their lifespan and efficiency.
Along with routine washing, routine examinations are crucial. Look for signs of wear or damage, such as hydrophobic properties decreasing or surface area blemishes. If essential, a light polish might be related to rejuvenate the covering without stripping it away.
Moreover, the application of a booster spray can enhance the covering's hydrophobic impacts and restore its gloss. more helpful hints This is specifically beneficial for coverings that have been in use for a prolonged duration. Ultimately, by adhering to these maintenance practices, one can dramatically extend the life of a ceramic finishing, making sure that it remains to provide optimal security against ecological variables and keep the visual appeal of the car.
Verdict

Comments on “Find specialized auto detailing to keep your car looking flawless.”